Lobe Pump is one kind of positive displacement pump which is often known as a rotary lobe pump. With the exception of the lobes’ design to nearly meet rather than touch and rotate one another, it is comparable to a gear pump. Numerous industries, including pulp and paper, chemicals, food, beverages, pharmaceuticals, and biotechnology, use lobe pumps. Because of their exceptional hygienic features, great efficiency, and dependability, they are well-liked in these many industries.
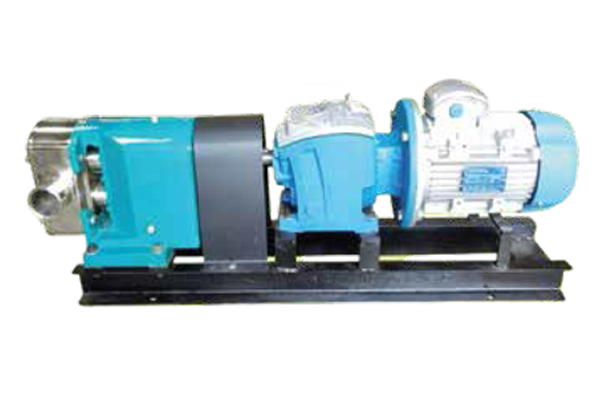
Rotary and Lobe Pump Features and Uses
Solids (such cherries and olives), slurries, pastes, and a range of liquids can all be handled by rotary pumps. They provide self-priming performance when wet. Product deterioration is reduced by a mild pumping movement. They can also run dry for short periods of time and provide both continuous and intermittent reversible flows. Additionally, flow is mostly unaffected by variations in process pressure, resulting in a steady and consistent output.
Because they can handle solids without causing harm to the product, lobe pumps are often utilised in culinary applications. Compared to other types of positive displacement pumps, lobe pumps may pump particles that are significantly bigger. This design performs less well when handling low viscosity liquids since the lobes do not make contact and the clearances are not as close as in other positive displacement pumps. Suction ability is poor, and loading characteristics are inferior to those of other designs. Reduced speeds are necessary to produce satisfactory results with high-viscosity liquids.
How Lobe Pump Works?
Lobe pumps function similarly to external gear pumps in that fluid circulates throughout the casing. However, the lobes do not come into contact, in contrast to external gear pumps. The gearbox contains external timing gears that avoid lobe contact. The gearbox houses the pump shaft support bearings. Because the bearings are not in contact with the pumped liquid, pressure is controlled by shaft deflection and bearing placement, which lowers the pump’s noise level. One type of rotational positive displacement pump is the lobe pump.
- The lobes produce an expanding volume on the pump’s inlet side when they emerge from the mesh. This cavity receives the material to be pumped, which may be a liquid, gas, or potentially tiny solid particles. Enclosed volumes of material are formed between the rotors and the pump casing when the lobes rotate past the inlet port.
- The material moves around the inside of the casing within the enclosed spaces formed between the rotor’s lobes and the casing itself, without flowing between the lobes.
- The meshing of the lobes on the pump’s discharge side blocks the pumped material from flowing back to the inlet. As the pumping continues, the material is pushed out through the outlet port. If there is a restriction at the discharge port, like releasing a large volume of air into an engine’s intake manifold, pressure builds up in the discharge area. However, a lobe pump does not actually compress the material it pumps.
Features
- The pump’s lobes do not come into contact with each other, lobe pumps can move solids suspended in slurries (such as cherries or olives in food processing applications) without product damage.
- The gentle pump action further minimizes product degradation.
- Can handle larger sized particles than may be pumped with other types of positive displacement pumps.
- May be easily cleaned using either clean-in-place (CIP) or steam-in-place (SIP) methods, making them ideal for hygienic processing applications.
- Highly efficient for pumping very viscous liquids.
- Offer accurate and consistent fluid output that is unaffected by changes in head pressure, assuming sufficient fluid viscosity.
- The fluid flow can be increased or decreased by controlling the drive speed.
- If wetted, rotary lobe pumps are also self-priming, and can run dry for long periods of time (assuming the pump’s seals are lubricated).
- Generally easy to maintain.
Range
Size: up to 3”
Flow: 15m3/hr.
Pressure: 7kg/cm2
Rpm: up to 960